Types of Transformers (and What They're Used For)
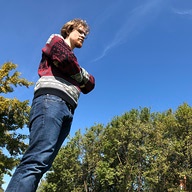
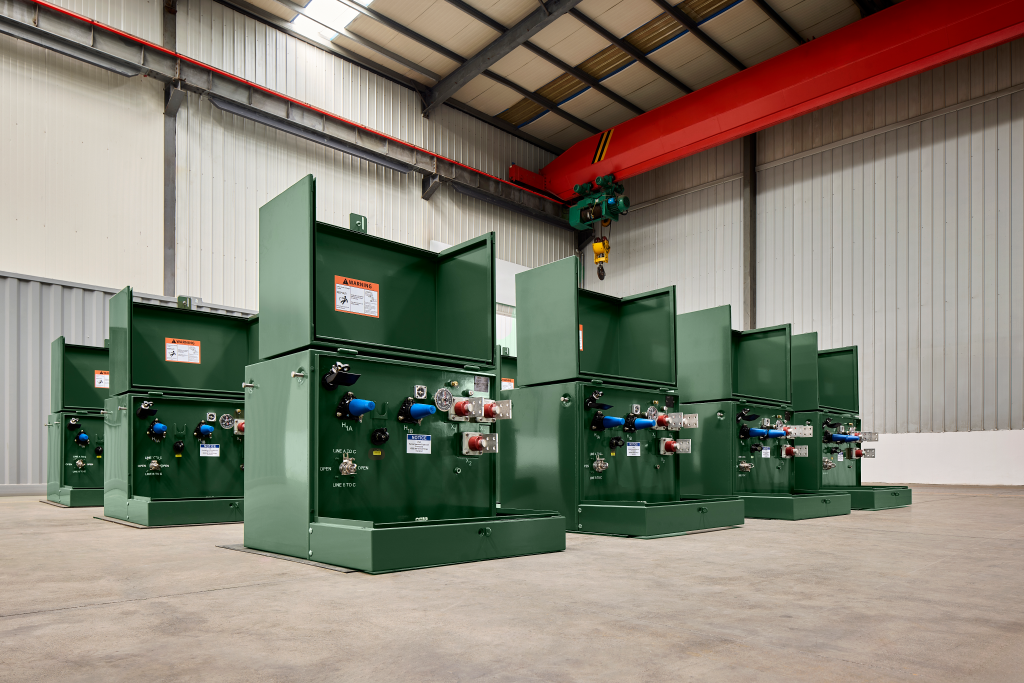
Types of Transformers (and What They're Used For)
When most people walk through Myeong-dong in Seoul, they're captivated by the dazzling LED billboards and neon signs that transform the shopping district into an electric wonderland. But while many marvel at the spectacular displays, I'm always that person whose mind wanders to the complex electrical infrastructure making it all possible.
This fascination isn't accidental. My journey from teaching in Korea to specializing in transformer technology was sparked by love – specifically, the need to find work in the United States so my Korean wife and I could build our future together. That career change led me to discover my true passion: the intricate physics of power distribution that keeps our modern world humming.
This article will guide you through different types of transformer classifications, showing you how the transformers powering urban shopping districts differ from those that power the homes we live in. I’ll also share my professional assessment of what's keeping those bright lights of Myeong-dong shining.
.jpeg)
Basic Transformer Concepts
Transformers are critical for efficient and reliable power distribution. They transfer electrical energy between circuits by electromagnetic induction and help modify voltage levels to meet the grid's demands.
Transformers operate on the principle of electromagnetic induction, where an alternating current in one coil generates a magnetic field that induces a voltage in a second coil. This mechanism allows transformers to transfer electrical energy between two or more circuits efficiently, without direct electrical connection.
The process of voltage transformation is helpful in electrical distribution systems. It enables increasing voltages for efficient long-distance transmission and reducing voltages for safe local distribution and consumer use.
Classification by Construction and Installation
Transformers can be categorized in several ways — construction and installation methods, voltage handling capabilities, cooling system design to name a few — and individual transformers often fit into multiple classification systems.
The physical construction and installation methods are one way to categorize transformers. This classification system focuses on how transformers are built and where they can be safely installed to meet specific environmental and accessibility requirements.
Padmount Transformers
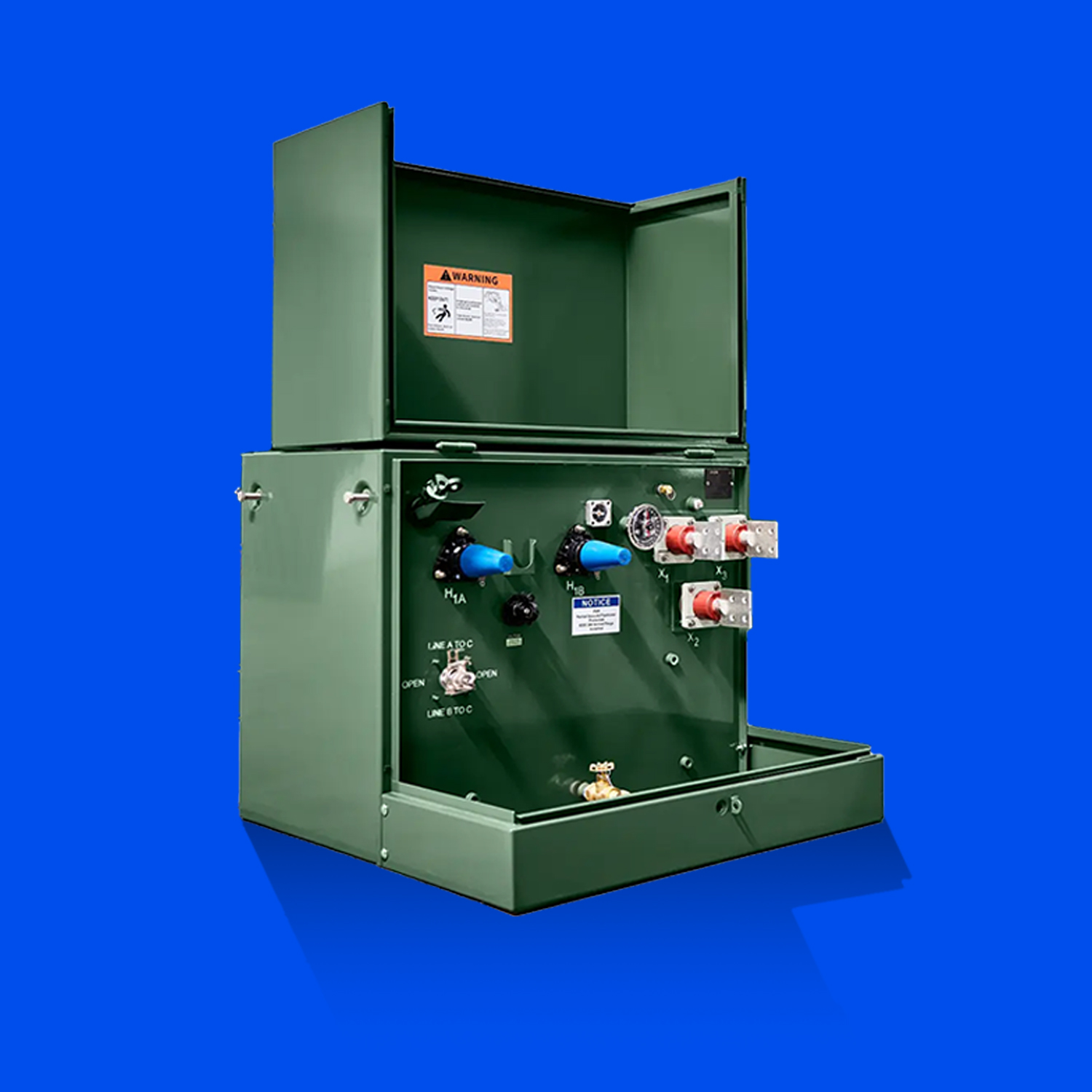
Padmount transformers are classified under construction and installation types because of their distinctive ground-level mounting design and protective enclosure construction. Their defining characteristics - the tamper-resistant steel housing and ground-level installation - directly reflect how they are built and where they can be safely installed.
Padmount transformers are commonly placed in residential neighborhoods or commercial areas where space efficiency and safety are concerns. Their ground-level installation does not require fenced enclosures and is less obtrusive than other transformer types.
The design of padmount transformers emphasizes maintenance accessibility and safety for utility workers. Their structure allows easy front and rear access to internal components, which facilitates quick inspections, maintenance, and repairs without significant disruptions.
Polemount Transformers
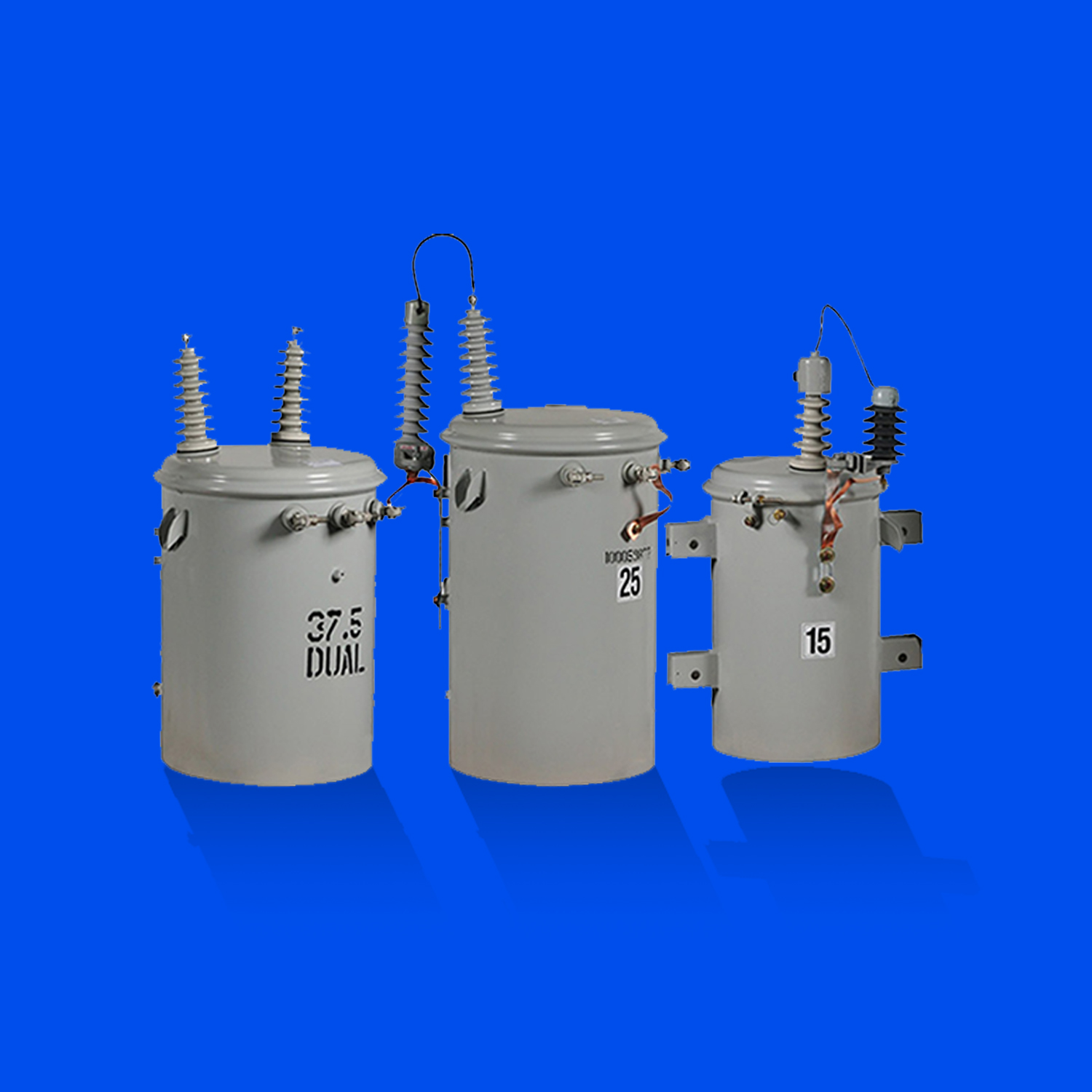
Polemount transformers fall into the construction and installation classification due to their specialized design for elevated mounting and their distinctive pole-attachment construction features. Their defining characteristic - the ability to be mounted on utility poles - is directly tied to both how they are built and how they must be installed.
They’re meant for electrical distribution in areas that are less densely populated, such as rural and suburban areas. Polemount transformers are positioned above ground on utility poles, they offer enhanced security by being less accessible, reducing the risk of tampering and vandalism. The elevated installation protects them from potential flood damage and adverse weather conditions.
While polemount transformers provide numerous benefits, they require specialized equipment like bucket trucks for maintenance, which can complicate and increase the cost of service.
Classification by Voltage Levels
Another way to classify transformers is by their voltage handling capabilities. And this classification system can be applied across different transformer types. Both padmount and polemount transformers can be designed to handle various voltage levels, for instance.
High Voltage Transformers
High voltage transformers earn their classification by their ability to handle voltage levels ranging from 69 kV to 765 kV and above.
They're designed specifically for transmission networks, where they efficiently transfer electricity over long distances to minimize losses (I²R). Their primary job is to step up voltage from power generating stations to levels suitable for long-distance transmission, and this voltage handling capability defines their role in the power distribution system and distinguishes them from other voltage classifications.
Given the high voltages, these transformers are designed with numerous safety features to protect the transformer and the surrounding infrastructure. These include advanced insulation materials, grounding methods, and protective relay systems to help manage faults effectively.
Medium Voltage Transformers
Medium voltage transformers bridge high voltage transmission lines and low voltage end-user applications. They handle voltage levels from about 5 kV to 69 kV, which is essential for commercial facilities, small manufacturing plants, and residential areas with high demand.
These transformers step down (decrease) high voltage to usable levels for local grids or utility networks. Their robust construction withstands local distribution network challenges, including weather impacts and industrial conditions.
Medium-voltage transformers are equipped with fault protection, thermal monitoring, and durable insulation for operational reliability and safety. They are commonly used in city substations, industrial parks, large residential complexes, hospitals, and universities.
Low Voltage Transformers
Low voltage transformers handle voltages below 1 kV for final-stage energy distribution to end-use applications in residential homes and small businesses. They step down medium voltage electricity to levels suitable for consumer appliances, lighting, and heating systems, ensuring safety and compatibility.
Low voltage transformers are typically smaller and prioritize safety. They are designed for easy installation and maintenance with features like plug-in connections and weatherproof casings. To prevent overloads, short circuits, and overheating, low voltage transformers include safety features such as thermal protectors, circuit breakers, and fuses.
Found in residential areas, commercial buildings, and light industrial sites, these transformers are essential for precise voltage regulation in computer networks and telecommunications equipment.
Classification by Turns Ratio
Transformers can also be classified by their ability to adjust voltage levels. It is based on turns ratio: the ratio of the number of turns in the primary winding to the number of turns in the secondary winding.
Step-Up Transformers
Step-up transformers are called such because they increase the voltage of electrical power while decreasing the current. They have a turns ratio greater than one — meaning the secondary coil has more turns than the primary coil.
Step-up transformers are essential for efficient long-distance power transmission. Higher voltages with lower currents reduce I²R losses, which typically occur as heat in power lines. Reducing these losses enhances the electrical grid's overall efficiency.
Step-up transformers are generally used at power generation plants, elevating the voltage from generated levels to high voltage for transmission across long distances.
Step-Down Transformers
Step-down transformers get their classification from having a turns ratio less than one — fewer turns in the secondary coil than the primary coil. Step-down transformers convert high voltage electricity from transmission lines to lower voltages suitable for end-user consumption in residential, commercial, and industrial settings.
Lower-voltage electricity is safe for everyday use, allowing appliances and other devices to be powered without posing hazards. Step-down transformers are commonly located on utility poles or underground lines to distribute power efficiently across urban and rural areas.
Classification by Cooling Methods
Transformers are categorized based on their cooling techniques, an important design element directly impacting a transformer’s ability to handle heat generated during operation.
Liquid-Filled Transformers
Liquid-filled transformers use cooling fluids to manage heat generated by transformer operation, which enhances efficiency and extends the service life. Commonly used fluids are:
- Mineral Oil: Widely used due to its excellent insulative properties and cost-effectiveness. However, it is flammable, requiring careful handling and specific safety measures.
- Silicone: Offers a higher flash point than mineral oil, reducing fire risk. Silicone is preferred in environments where fire safety is a major concern.
- FR3 (Bio-based Fluid): A newer, environmentally friendly option that provides superior fire resistance and biodegradability compared to mineral oil, enhancing operational safety and environmental protection.
Liquid-filled transformers are common in urban and industrial areas where high cooling efficiency is necessary to handle large loads safely. Their superior cooling capability increases operational loads and reliability.
Dry-Type Transformers

Dry-type transformers use air for cooling, avoiding the risks associated with liquid coolants, making them ideal for indoor or environmentally sensitive areas. They employ natural air cooling (AN), where convection from the transformer’s heat drives air movement, and forced air cooling (AF), which uses fans to enhance cooling efficiency under high load conditions.
Dry-type transformers are constructed with ventilated enclosures and materials with high thermal conductivity to maximize heat dissipation. Designed without liquid, dry-type transformers significantly reduce fire hazards, eliminate fluid leaks, and do not emit toxic gases during fires. They are suitable for use in schools, hospitals, and shopping centers. Their maintenance is minimal due to durable construction and spatial arrangements that optimize air circulation around critical components.
Classification by Core
Transformers can be classified according to the type of core material used in their construction. The core material influences the transformer’s magnetic properties, affecting its performance characteristics and the applications for which it is best suited.
Iron Core Transformers
Iron core transformers have cores made from ferromagnetic materials like silicon steel laminations, which have excellent magnetic properties. They are highly permeable to magnetic flux and have low hysteresis losses (energy loss as heat in changing magnetic field).
Iron core transformers are commonly used in residential and commercial settings, typically to step down high voltages suitable for residential use and to adjust power levels in industrial facilities. They are durable and highly efficient, reducing operational costs and supporting sustainability by lowering carbon emissions.
Ferrite Core Transformers
Ferrite core transformers are designed for high-frequency applications in electronics and telecommunications. Ferrite cores are made from ceramic magnetic materials composed of iron oxides mixed with metallic elements like nickel, zinc, and manganese.
Ceramic magnetic materials have very high magnetic permeability and low electrical conductivity, which reduces eddy current losses prevalent at higher frequencies. These properties make them highly effective in handling rapid magnetic flux changes associated with high frequencies.
Ferrite core transformers are predominantly used in switch-mode power supplies, integral to virtually all electronic devices, from computers and televisions to mobile phones. They are also essential in other high-frequency applications, including RF (radio frequency) and microwave devices.
Air Core Transformers
Air core transformers use air or another non-magnetic material as the core. Because they lack a solid core, they eliminate core losses like hysteresis and eddy currents associated with iron or ferrite cores. They also have a low impedance per turn. These features allow more efficient operation at high frequencies where rapid magnetic field changes occur frequently.
Air core transformers are commonly used in high frequency applications, radio transmission equipment, RF circuits, and medical devices. They are suited for applications where impedance matching is essential to optimize power transfer and maintain signal integrity.
Toroidal Core Transformers
Toroidal core transformers with donut-shaped cores excel at reducing magnetic leakage and operational noise. The continuous, symmetrical shape of the toroidal core effectively confines the magnetic field, minimizing electromagnetic interference and enhancing energy efficiency. This feature is beneficial in audio applications, where it helps reduce hum noise and ensure cleaner sound reproduction.
Toroidal transformers are commonly used in audio and sensitive electronic circuits. Their compact and lightweight design makes them suitable for space-constrained applications like consumer electronics and medical devices.
Classification by Phases
The number of phases transformers use directly impacts their application and efficiency in various settings.
Single-Phase Transformers
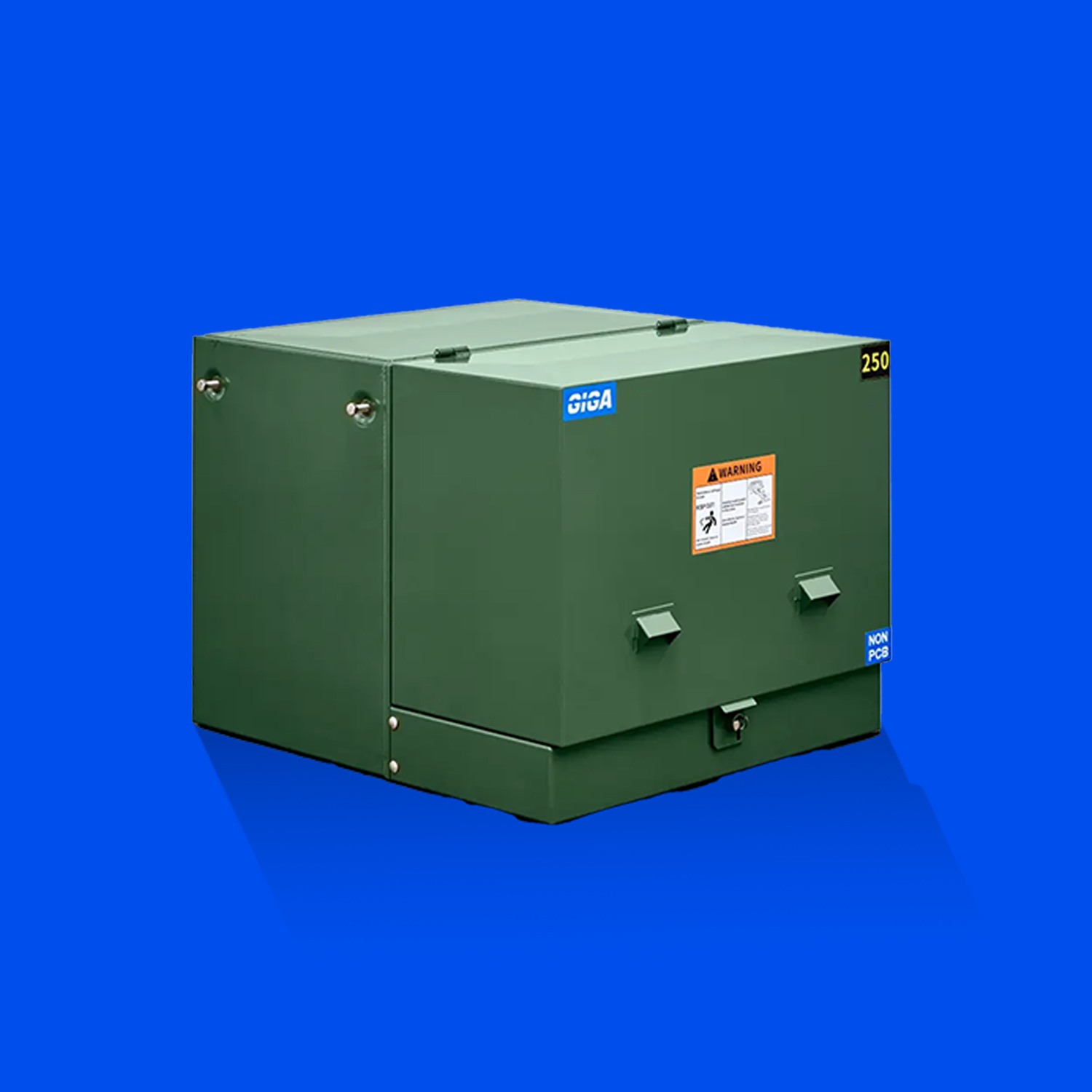
Single-phase transformers are simple, cost-effective, and efficient at handling lower power loads. They are used in homes and small businesses to distribute electricity to appliances, heating, lighting, and basic machinery. Their fewer components and connections make them less expensive to manufacture and maintain, reducing operational and repair costs.
Three-Phase Transformers
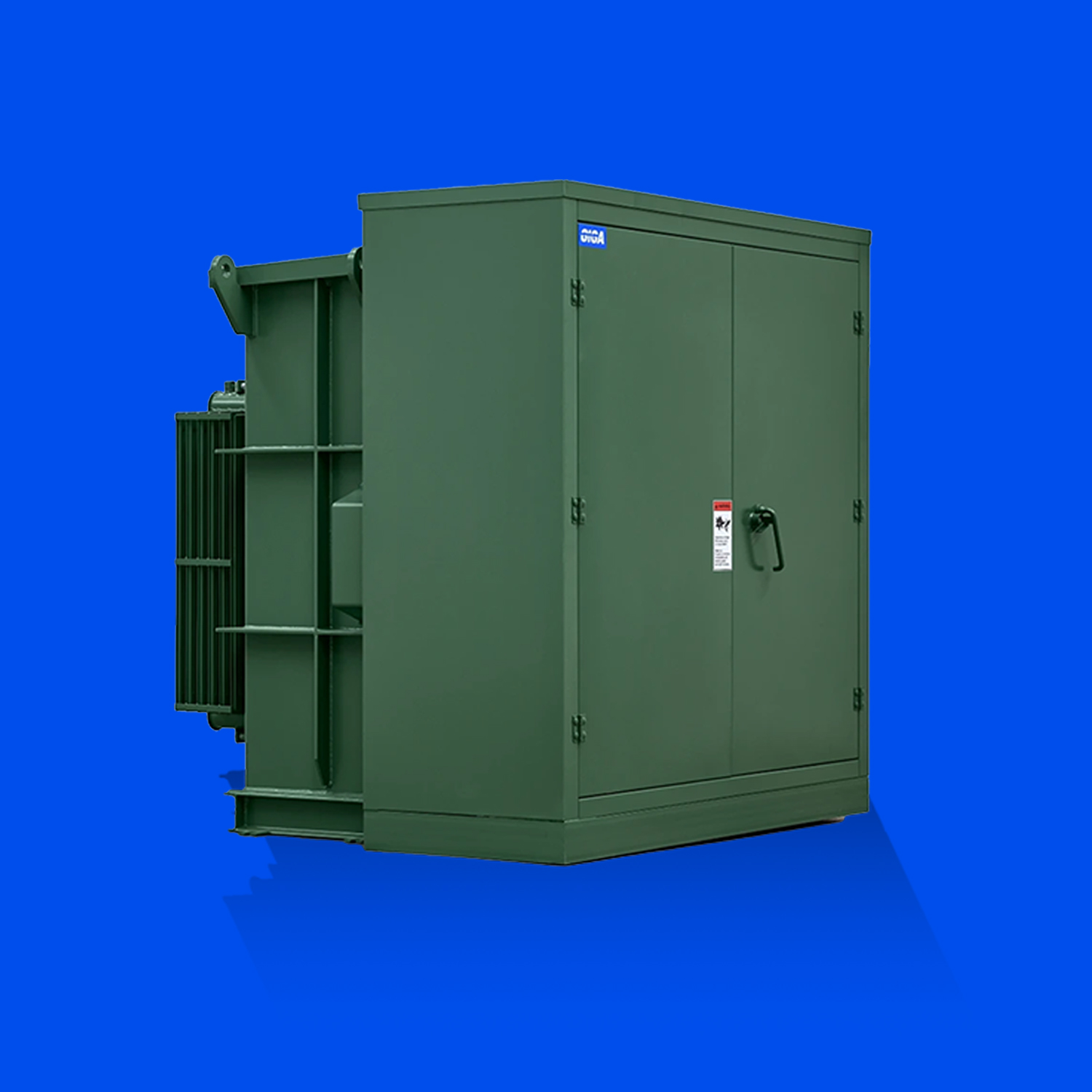
Three-phase transformers are used in industrial, large commercial environments, manufacturing plants, and heavy industries like automotive and mining. They offer superior power handling capabilities and efficiency for high-demand applications. By providing uniform power and preventing lags or surges, they support heavy machinery. They are more compact and energy-efficient than single-phase transformers, using less conductor material for the same power capacity.
Classification by Winding Arrangement
The winding arrangement in a transformer influences its voltage regulation, efficiency, and the degree of electrical isolation it can provide.
Autotransformers
Autotransformers have a single continuous winding that serves as primary and secondary windings. The design reduces material needs and construction complexity, lowering manufacturing and maintenance costs. Their efficient design optimizes copper usage, which enables them to handle higher currents with reduced resistive losses.
Autotransformers are ideal for applications needing slight voltage adjustments, such as voltage boosting in long distribution lines, railway traction, and starter transformers for induction motors. However, they do not provide electrical isolation between primary and secondary circuits, which creates the risk of electrical shocks, interference, and system failures.
Dual Winding Transformers
Dual winding transformers have separate primary and secondary windings. They provide better voltage regulation and complete electrical isolation to protect sensitive electronic equipment from power disturbances and enhance safety. This separation prevents faults from transferring between circuits in medical facilities and data centers.
Dual winding transformers enable precise voltage control under varying load conditions, offering consistent operation of industrial machinery. Their design is suitable for harsh conditions, making them widely used in commercial and industrial settings.
Specialized Transformer Types
Beyond the basic classifications, there are specialized transformers designed to meet specific industrial tasks and requirements.
Instrumentation Transformers
Instrumentation transformers help measure and ensure safety within electrical systems. They transform high voltages or currents to lower levels that are manageable by measurement devices. They monitor and control electrical systems, providing real-time data while safely isolating measurement devices from high-power circuits.
Instrumentation transformers protect equipment and personnel by preventing high-voltage faults from affecting measurement systems. They are used in utility grids, industrial automation, and various industries such as manufacturing and energy.
Distribution Transformers
Distribution transformers are vital in electrical grids, efficiently stepping down voltage from transmission to utilization levels. They minimize energy loss and operational costs while enhancing system reliability.
Urban transformers incorporate advanced load management features to accommodate high demand in compact spaces, whereas rural transformers are robust and designed for longer distances and environmental resilience.
Substation Transformers

Substation transformers are integral to energy infrastructure, managing high voltages and large power flows essential for industrial areas and electrical grids. They step down high voltages from transmission lines to levels suitable for distribution.
They are used in substations that serve industrial complexes and power distribution grids. They commonly have robust insulation, advanced cooling systems, and fault protection to enhance safety and operational continuity.
Transformer Applications
Transformers are key in managing and distributing electrical power, efficiently meeting the specific needs of different sectors.
Industrial Use
In industrial settings, transformers power heavy machinery and support large-scale operations. They are equipped with fault protection, durable materials, and cooling systems to handle high electrical loads to keep manufacturing and processing plants running smoothly.
Commonly used three-phase transformers provide consistent power for large motors, while high-voltage transformers safely step down transmission levels for industrial use. These features help minimize energy loss, cut operational costs, and enhance safety by reducing the risk of accidents.
Commercial Use
Transformers in commercial settings support operations from small shops to large office buildings, focusing on reliability and cost-efficiency. They vary widely to fit different scales of operation, from compact single-phase transformers in small stores to robust three-phase systems in large complexes.
Efficient transformers are key to managing energy, reducing wastage, and lowering utility bills. Custom solutions are often needed, especially in urban areas where space is limited, ensuring transformers integrate into specific commercial environments without compromising performance.
Residential Use
In residential areas, transformers convert high voltage electricity from utility lines to safer levels suitable for home use. Step-down transformers, such as polemount and padmount types, are commonly used.
Polemount transformers serve larger areas from utility poles, while padmount transformers are placed at ground level in neighborhoods for safety and minimal visual impact. Transformers in residential areas are designed to operate quietly and blend aesthetically with their surroundings to minimize noise and visual disturbances in residential settings.
Advanced Transformer Technologies
Transformer technologies are evolving to improve the efficiency, sustainability, and adaptability of electrical grids for modern energy needs. Emerging trends focus on integrating renewable energy, reducing environmental impact, and leveraging advanced technologies like digital twins for real-time diagnostics and predictive maintenance.
The following sections highlight three cutting-edge innovations shaping the future of transformer technology: smart transformers, green transformers, and solid-state transformers.
Smart Transformers
Smart transformers enhance power distribution with real-time monitoring and predictive maintenance using Internet of Things (IoT) technology. They optimize grid performance by automatically adjusting voltage and power quality according to changes in demand.
Smart transformers help maintain grid stability and improve efficiency, especially when fluctuating renewable energy sources like solar and wind are integrated. They reduce maintenance costs, extend lifespans, and support a sustainable energy system.
Green Transformers
Green transformers focus on sustainability using eco-friendly materials like biodegradable cooling liquids from vegetable oils and recyclable construction materials. These transformers operate more efficiently, reducing energy loss and carbon footprint.
Green transformers comply with stringent environmental regulations, ensuring global marketability while contributing to energy savings and emission reductions.
Solid-State Transformers
Solid-state transformers (SSTs) use semiconductor components for efficient voltage conversion. They are compact in design and reduce energy losses compared to traditional transformers. SSTs provide advanced features like dynamic voltage regulation, renewable energy integration, and enhanced power quality management, all of which improve grid stability.
SSTs support real-time power management in smart grids and are ideal for space-constrained urban areas and electric vehicle charging infrastructure. They are still in the research phase, but as SST technology evolves, it promises to make power distribution more efficient and flexible.
Maximizing Efficiency with the Right Transformer
Now, circling back to the electrical infrastructure powering Myeong-dong. By my (rough) estimate, Myeong-dong requires approximately 250,000 kWh daily to power its digital billboards, neon displays, retail establishments, and entertainment venues. This power is distributed through strategically placed high-capacity transformers (3,000-5,000 kVA), utilizing both polemount and padmount configurations. The system is likely managed by a central substation, incorporating voltage regulators and advanced energy management systems. To meet these demanding power requirements effectively and safely, specialized transformer solutions are essential.
Giga Energy specializes in customized transformer solutions that meet or exceed NEMA, ANSI, IEEE, and DOE standards. Our comprehensive range includes padmount, polemount, dry-type, and substation transformers, engineered for optimal performance across commercial, residential, and industrial applications.
I work with engineering teams daily on custom transformer specs. Reach out on LinkedIn or contact our team to discuss your upcoming projects.
Get a Transformer Quote
Provide us with your specific requirements to receive an immediate quote tailored to your needs.